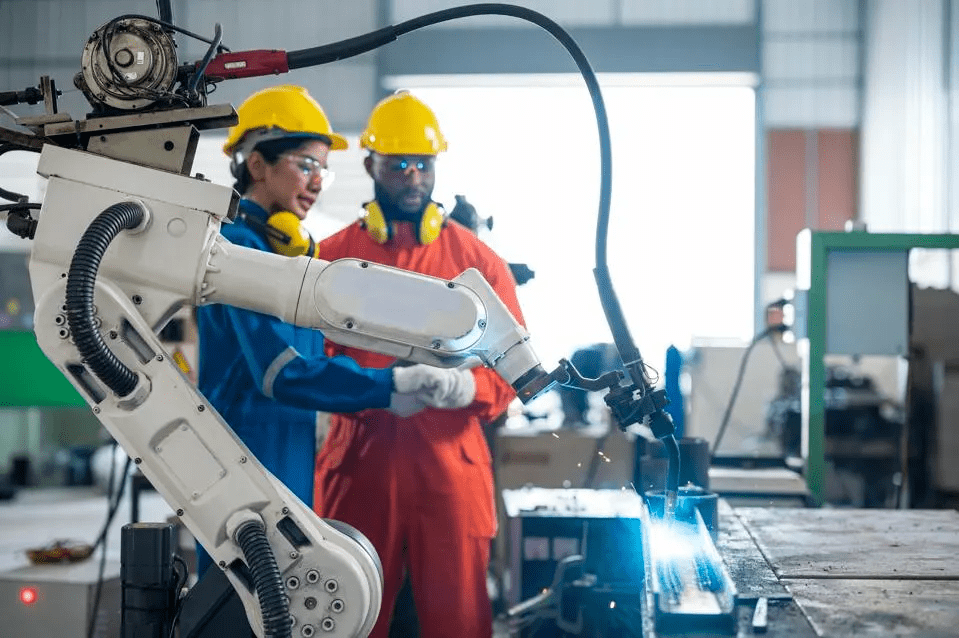
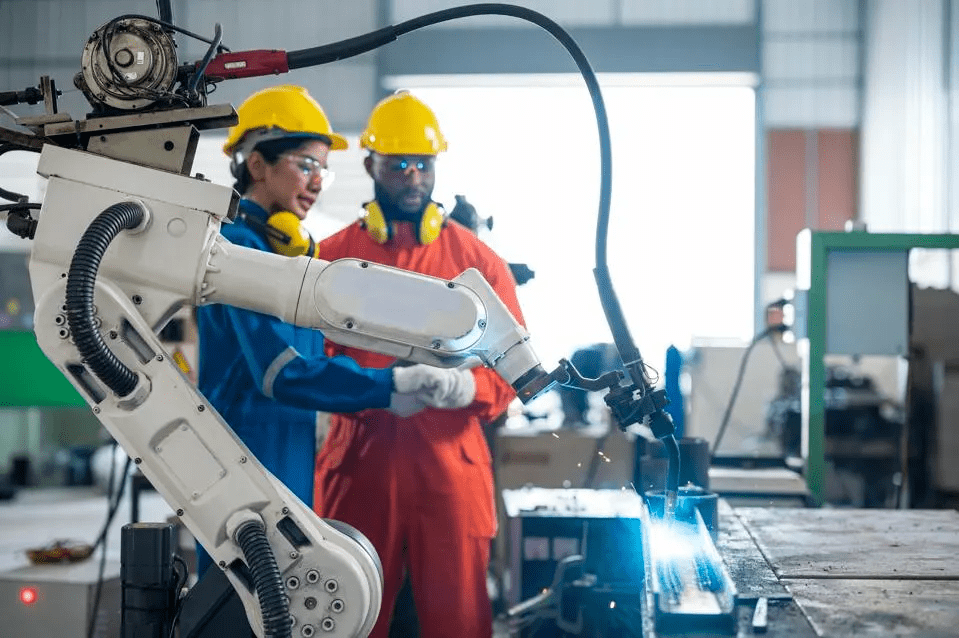
Many of us have seen photos of and read stories about robots working on the production floor in factories, speeding up old-school assembly lines to build products more quickly. And while the robotics trend in manufacturing is continuing to grow, that’s not the only way technology (including artificial intelligence) and automation are impacting the industry.
From enhancing worker safety to more efficiently moving goods and materials from point A to point B, automation is making its mark on the manufacturing industry, and tech experts expect even more changes and improvements in the near future. Below, 17 members of Forbes Technology Council discuss specific manufacturing tasks that are (or soon will be) handled more efficiently, safely and productively by technology and automation.
1. Automated Decision Workflows
Manufacturing is rapidly retooling its digital infrastructure to support more agile product development, sourcing and reporting activities, accelerated by changing customer demands, regulations and supply shortages. Integrating external data, connecting data silos and delivering automated decision workflows are top levers to accelerating development, reducing costs and mitigating business risk. – Neil D’Souza, Makersite
2. Quality Assurance
Through AI, the manufacturing industry is converting the “art of what’s possible” to the “art of what’s real.” Functions including quality assurance on the shop floor and supply chain resiliency have seen positive outcomes through automation—for example, AI-powered wrinkle identification in car seat assembly lines. With the advent of generative AI, possibilities will now rapidly expand into assistive or augmentative use cases for multiple personas. – Naresh Mehta, Tata Consultancy Services Ltd.
3. Pricing Life Cycles
Through automation, we’re seeing new levels of sophistication when it comes to managing pricing life cycles. The ability to quickly analyze huge amounts of customer data, easily update prices, and streamline sales negotiations or self-service buying gives us significantly more agility in responding to market changes. AI-powered pricing processes allow modern manufacturing firms to unlock new efficiencies and strategies. – Pascal Yammine, Zilliant
4. Repetitive Tasks
Automation is speeding up factories! Machines can now take care of repetitive tasks that traditionally had to be performed by workers. Smart machines are becoming more prevalent in factories, increasing production and reducing errors. As we progress further, these smart machines are bound to enable further automation by penetrating beyond the assembly lines. – Vamsi Tammana
5. Machine Monitoring
Manufacturers can leverage AI tools that send automated alerts to maintenance about machine faults so they can make repairs and avoid unplanned downtime. We’ve seen such tools boost ROI, help teams meet production goals and cut waste. Industrial AI is evolving every day, with tools becoming true copilots for plant workers. Manufacturers should consult with startups so that new AI tools can be developed in response to their evolving business needs. – Saar Yoskovitz, Augury
6. Productivity And Quality Enhancement
Automation has been a key to evolution, driving transformation through improved quality, cost efficiency and operational optimization. The integration of modern sensors and robotics, combined with the analysis of the data produced by these devices, helps manufacturers harness insights and drive enhancements in productivity and quality. These capabilities serve as the foundation for expansion that leverages AI. – Kim Bozzella, Protiviti
7. Hazardous Work
Automation and robotics are elevating manufacturing to the next level by eliminating a lot of human labor—especially tasks that are dirty, dangerous or monotonous. Developments such as Tesla’s humanoid Optimus bots signal a future where robots can handle intricate tasks, a trend likely to evolve and expand further in manufacturing. – Steve Richmond, Projetech
8. Standardized Processes
Automation has had a stabilizing effect on manufacturing, as it has standardized processes and made data insights more available for decision making. Standardized processes help manufacturers predict production times, and with automated data collection, manufacturers will gain deeper insights into every stage of production and more easily reduce inefficiencies and product defects over time. – Bill Rokos, Parsec Automation
9. Nearshoring Models
Automation is lowering the amount of human labor needed for various aspects of production. As this happens, the advantage that moving work offshore offered—reduced labor costs—is no longer a driver for manufacturers, as shipping and logistics expenses now make up a larger portion of the bottom line. This will lead companies to move to a nearshoring model, making manufacturing local once again. – Josh Dunham, Reveel
10. Centralized Data
Automation has enabled manufacturers to activate decades of stagnant data that used to be stored across various disparate locations. Manufacturers that centralize their data are now putting AI and data analytics to work on new use cases, such as predicting operational inefficiencies and pinpointing anomalies in complex processes, significantly improving productivity and quality—benefits that extend to the customer. – Marco Santos, GFT
11. Bespoke Product Runs
Automation has made it possible to make special, one-of-a-kind products quickly and in large amounts, mixing the best of both worlds—manufacturers can make lots of items efficiently while still providing what each customer wants. This capability is expected to improve and be leveraged more widely, enabling factory teams to be more flexible and creative. – Margarita Simonova, ILoveMyQA
12. Just-In-Time Inventory Management
Logistics management and automated ordering have significantly reduced parts inventories in factories. Over the past decades, we have seen manufacturers’ inventories go from on-site warehouses to palettes on the production floor. The past five years have moved just-in-time management from the trailer to the machine. With AI and better supply chain prediction, I’d anticipate even shorter lead times. – Kevin Korte, Univention
13. Autonomous Material Transport
Progress in autonomous material transport has refined manufacturing processes, as drones and self-operating vehicles now efficiently move goods. This reduces the need for human handling of dangerous tasks and bolsters logistical operations. Anticipated advancements in this domain are likely to further adoption and hone navigational capabilities, thereby increasing the flexibility of production lines. – Jagadish Gokavarapu, Wissen Infotech
14. Eco-Friendly Practices
Automation has revolutionized the manufacturing industry by facilitating the adoption of eco-friendly practices. From energy-efficient robotic systems to waste-reducing automated processes, manufacturers can now minimize their environmental footprint while optimizing productivity. This trend will likely expand further as sustainability becomes a top priority for consumers and businesses. – Cristian Randieri, Intellisystem Technologies
15. Worker-Directed Process Improvements
Digital twins are mapping entire manufacturing plants with various sensors, enhancing the data flowing from the factory floor. The capabilities are astounding, and I see this trend exponentially enhancing how we work and create products in the factory. More and more workers will be able to use technology to make changes on the floor, improve efficiency or increase production. – Hadi Tabani, Liquid Technologies
16. 3D-Printed Products
3D printing has revolutionized how products are designed and produced, allowing for more complex designs and rapid prototyping. This speeds up the development process and enables customization in manufacturing at a lower cost. 3D printing technology will continuously evolve, becoming more accessible and versatile and impacting various sectors within manufacturing. – Gergo Vari, Lensa, Inc.
17. Collaborative Automation
AI and advancements in sensory technology have spurred the adoption of cobots in manufacturing, enhancing safety and teamwork with humans. These robots quickly learn and adapt through observation, signaling a shift toward more intelligent, collaborative automation, with the potential for further growth in the sector. – Jo Debecker, Wipro
Source: forbes.com
Leave a Comment